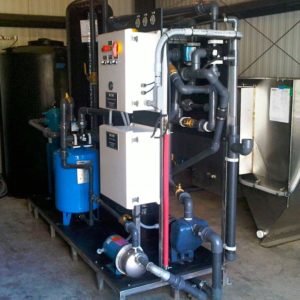
Oil and gas drilling, including hydraulic fracking, is a complicated endeavor. The nature of the work ensures that dirt, downhole acids, crude residues, waxes, and grease coat down-hole motors, pumps, subs, drill pipe, tanks, and vehicles. Constant washing and NDT testing is essential to maintaining the equipment in good working order. These processes, however, produce an enormous amount of water. Often, the wastewater is stored onsite and disposed of every few weeks – which can get very expensive.
To reduce both hauling costs and water usage, many oil field services companies have installed our Drilling Equipment (DE Series) Systems to treat and recycle their wastewater. Robustly designed and manufactured for the oil and gas industry, our heavy-duty, multi-stage treatment systems clean up the water for re-use or discharge. By simplifying the water handling, many clients are able to both increase production and reduce costs, resulting in pay back periods of only months!
The important first stage is the solids handling system. Depending on the amount of solids and the wash pad design, our engineers will develop a site-specific system to remove as many solids as possible before the water goes to the filtration systems.
The next stage of the system is the stainless steel clarifier oil water separator which removes most suspended solids (TSS), essentially all settleable solids and all free and dispersed non-emulsified oils from the waste stream.
Depending on the application, the next stage could be biological treatment. Our proprietary biological filter system uses a revolutionary, patented US technology, including specifically developed microbes combined with a highly efficient aeration technology, to treat the water and remove substantially all of the COD and FOG in the water.
In the final polishing stage, the water goes through an extremely efficient filtration process utilizing fully automated solids filtration and a proprietary blended activated carbon (GAC) polishing filtration, and a corona discharge ozone generator to prevent odors. Processed water passing through the system will be free of particles greater than 10 microns in size, substantially all emulsified oils, waxes and other volatile organic compounds.
STANDARD DE Series SYSTEM FEATURES:
- Stainless Steel Construction
- High-Efficiency Pumps
- Corona Discharge Ozonation System
- Solids Handling & Separation
- TSS, COD, FOG Reduction
- Multi-Stage / Multi-Pass Filtration
- Pressurized Blended Carbon Polishing Filters
- Auto-Backwashing Filters
- NEMA 4X Control Panel with PLC controller
Depending on the location, many options are available to maximize the efficiency of the wastewater treatment system including:
OPTIONAL FEATURES:
- SCADA and remote monitoring
- UL/CSA Listing
- Transportable equipment rooms
- Rain Diverter Systems
- Biological Treatment
- Rain Water Harvesting Systems
- Chemical/Acid/Salinity Resistant Pumps & Components
- ORP / pH/ Salinity control system
DE SERIES SYSTEM SPECIFICATIONS
MODEL | DE 10/10 | DE-30/20 | DE-60/50 | DE-100 | DE-200 |
---|---|---|---|---|---|
FLOW RATE, GPM | 1-10 | 1-30 | 10-60 | 30-100 | 60-200 |
COALESCING MEDIA, CUBIC FT | 4 | 8 | 24 | 48 | 96 |
CARBON BLEND MEDIA, CUBIC FT | 6 | 18 | 50 | 100 | 200 |
RE-CIRCULATION PUMP, HP | 1.5 | 3 | 3 | 5 | 5 |
RE-PRESSURIZATION PUMP, HP | 1 | 3 | 5 | 7.5 | 10 |
OZONE SYSTEM | Up to 32 grams of ozone per hour | ||||
CONTROL SYSTEM | PLC, Automatic, Manual or Off | ||||
PUMP FRAME SIZE | 34” W X 66” L | 34” W X 96” L | |||
POWER REQUIREMENTS | 208 / 240 v 1 ph or 208 / 240 / 480 v 3 ph | ||||
* LARGER CAPACITY SYSTEMS (500-1500 GPM) ARE AVAILABLE |