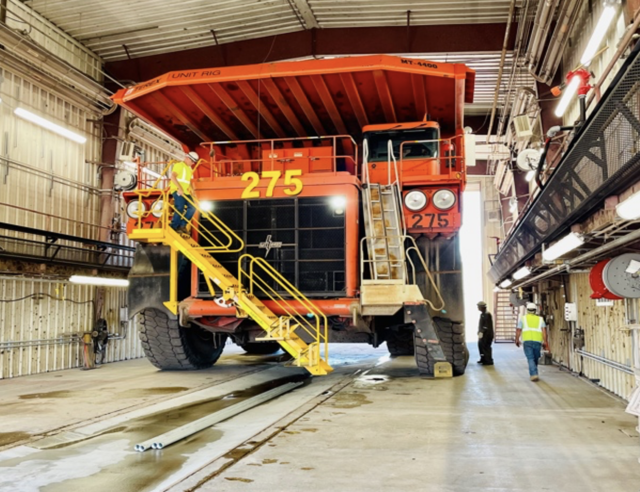
Mining equipment washing applications are challenging for several reasons. Aside from the fact that they are very large, mining trucks are difficult to clean. So, for generations, people just used fire hoses to clean the trucks. This meant pumping hundreds of gallons of water per minute to knock off as much dirt and rocks as possible.
But we are changing that with new highly efficient systems that use less water. This is very important since most mine locations are often remote with no sewer connections and are ALSO adjacent to environmentally sensitive areas.
MINING TRUCK WASHING SOLUTIONS:
With our systems, washing is done with a limited amount of water. Typically, we recommend three separate systems: a cold water monitor, a cold water demucker and a heated electric pressure washer.
Water Cannons / Monitors – Cold water monitors placed on rails or stands on the mezzanines initially wash the side and top of the trucks. The monitors will have 360° horizontal rotation and 135° vertical rotation, -45° to +90°. The monitors have variable flow nozzles that typically provide 100 GPM of water @ 100 PSI (378.5 LPM @ 689kPa). Typically, only one monitor is used at a time.
Demuckers – Demucking station reels are placed on the wash bay floor on either side of the wash bay. The hand-held demuckers can provide 20 GPM of water @ 1000 PSI (75.7 LPM @ 6895 kPa). By moving around the truck, operators can remove any dirt and solids missed by the monitors. Typically, one or two demuckers are used at a time.
Both the monitors and demuckers have remote start/stop control panels to permit an operator to control the pump operation. These NEMA-4X control panels include a momentary start switch and emergency stop switch; the start switch initiates a timer in the main control panel to run the pump for a pre-set time period to prevent unintended continuous operation.
Heated Pressure Washers – A heated pressure washer is used for a final wash, degreasing wash or de-icing. Pressure washer reels are be placed on the wash bay floor on either side of the wash bay. Typically, the pressure washer provide 5.4 GPM of water @3000 PSI (20.4 LPM @ 20684 kPa) with 72KW of heat. These systems use a trigger gun activated start/stop with time-delayed shut down.
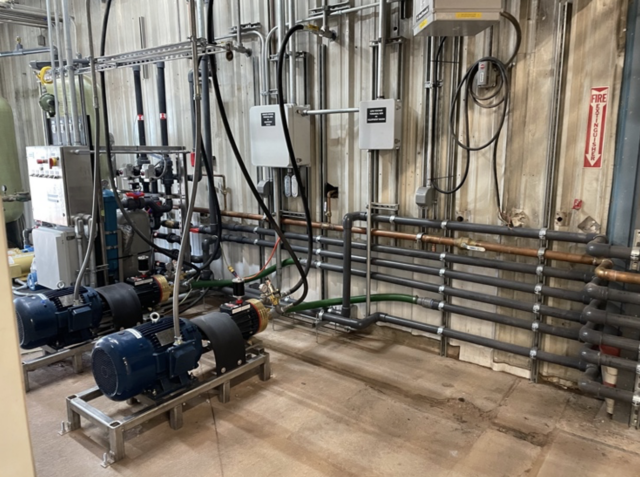
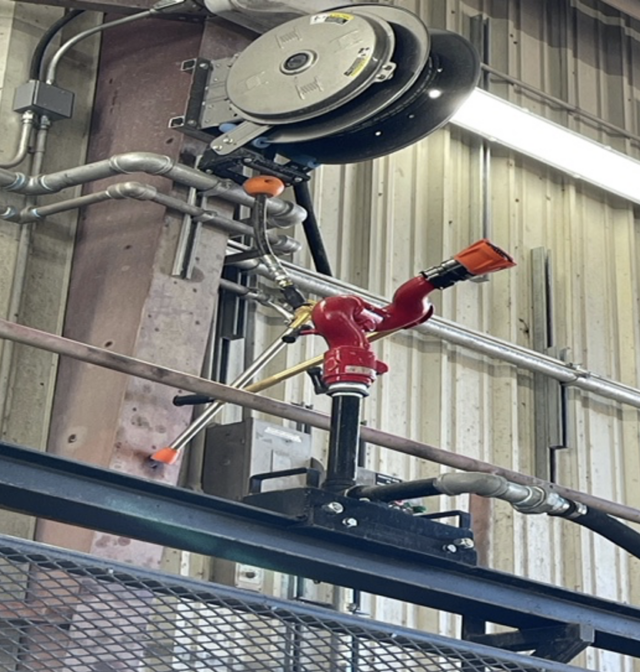
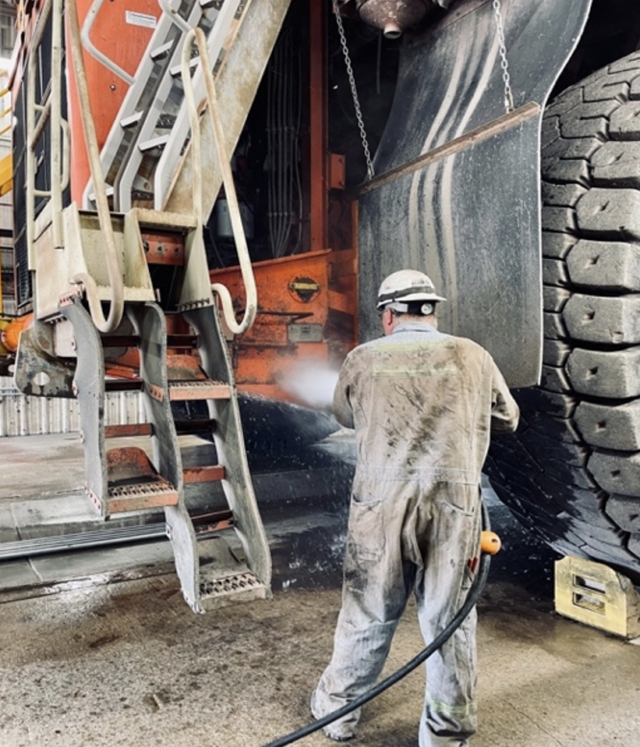
MINING TRUCK WATER TREATMENT SYSTEMS
The first step in water treatment is solids handling so we help design the best solids settling basin for your particular facility. Water treatment is typically done with a CT-Series wash water reclaim system with closed loop recycling system, capable of processing about 100 GPM (378.5 LPM). The system includes a clarifier oil water separator, fully automated solids filtration, activated carbon (GAC) filtration, an ozone generator, and a polishing filter to treat the water and prevent odors.
The system is designed to be completely closed-loop with no external discharge. It constantly re-circulates water from the raw water tank through the media filter, ozone injector and to the clean water tank. The process generally flows as follows:
- The water from the wash pad floor initially flows into a two compartment solids collection sump which will be cleaned out periodically. From the sump, a positive displacement pump will pump the water to a clarifier oil water separator which removes suspended solids, oils and greases.
- From the clarifier separator, water is pumped to a tank and then pumped to the recycle section of the CT filtration system where the water is filtered through a sand media filter, ozonated to reduce odor, and then directed to a second tank. Water is constantly circulated from Tank 1 through the CT Filtration system, and then to Tank 2. The cold water monitor system and demuckers are fed from Tank 2.
- In the secondary filtration section of the CT system, the fluid is then routed through tertiary filtration that includes a carbon bed to remove emulsified oils and soaps and a final filter to remove solids down to 20 microns. When the pressure washer requires water, the pump will provide cleansed, treated water for usage.
- An automatic backwash in the CT system occurs daily to prevent the sand and carbon filters from plugging with fines.
All equipment can be installed in a complete 40’ long transportable equipment room (TER-40HC). This will save on building and installation costs, provide protection from the weather and allow you to move the equipment to a different facility if the need arises.
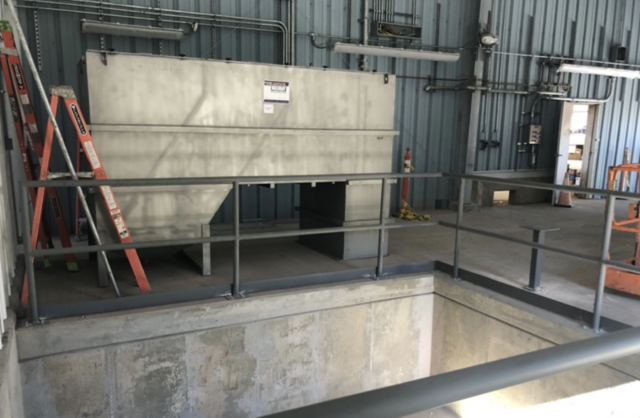
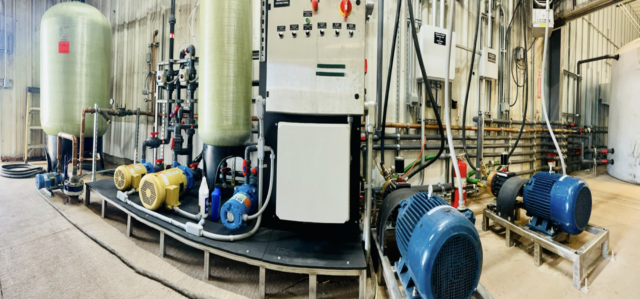