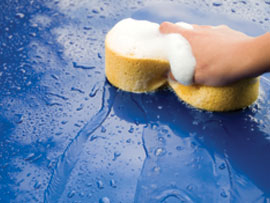
If you are a professional detailer, you are passionate about cars and trucks – making them look their best for their owners. Detailing involves hand cleaning, polishing and protecting the interior and exterior of cars and trucks. For an average vehicle, detailers usually hand wash or pressure wash and generate a relatively limited amount of oily, dirty water.
With this small amount of water, you are probably wondering why you need an oil water separator at all. The answer is simple. Your municipality or state requires that any water discharged into the sewer system or waterway not contain any oils that could either contaminate their waste water treatment plant or harm the environment.
Oil Water Separator Systems
In most locations, we can usually recommend a simple oil water separator system to satisfy even the tightest sewer restrictions. Our above ground stainless steel parallel-corrugated plate oil water separators will remove essentially 100% of all free and dispersed non-emulsified oil droplets larger than 60 microns in diameter with a specific gravity of .90 or less.
Coordination with Local Environmental Officials
If you are building a new facility, we will work with you to develop a simple, cost-effective system and coordinate with the local sewer authority or environmental officials to get everything approved.
We can provide analysis, which indicates that, at the calculated overflow rate, the separator will be provided with the required square feet of projected plate separation area to achieve the specified performance under laminar flow (i.e. Reynolds Number of less than 500) conditions. If required, calculations signed by a registered professional engineer can be provided for an additional fee.
Leasing Programs
These days, preserving capital and existing lines of credit are very important to many small and large businesses alike. We partner with Crest Capital to offer flexible, Application-Only leasing programs. It is quick and easy to apply. » Apply Now
Give us a call at 800-453-8639 to see if we can help you out.