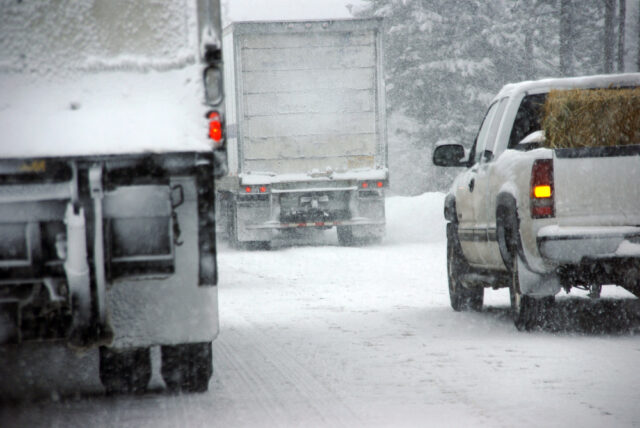
During the winter as winter storms approach, many municipalities will spread salt directly on the roads. Additionally, many have started to proactively apply what are called anti-icing fluids to prevent water from forming frost on the pavement surface. Whether anti-ice or deicing fluids, they all share the same basic chemistry, which is some form of salt. The formulations include sodium chloride, calcium chloride or magnesium chloride. Additionally, the anti-icing fluids often include organics such as beet juice or cheese whey.
This presents a unique issue for winter washing operations, especially when closed loop wash water treatment systems are employed. Closed loop wash water treatment systems are used in a variety of instances including no access to public sewer systems, unreasonable permitting issues associated with sending water to the sewer, and uneconomic costs to tie into a sewer system due to the distances.
When cars and trucks are driving on roads coated with either deicing or anti-icing fluids, the vehicle’s body will often become covered with a thin coating of salts. During typical washing operations, the salt is flushed off. If the wash bay is connected directly to a sewer, that salty water is diluted and simply sent to the city without issues. However, if the wash system is connected to a closed loop system where that water is used over and over, the salt levels will continue to rise in the wash waters. This leads to the salt being reapplied to the vehicle, which show up as salt streaks when it is dried. But more important than the streaks, the salt residue enhances the corrosion process on the metal.
There is no simple or inexpensive way to remove salts from wash waters. One option is to haul off or send a portion of the salt contaminated water to a city sewer. Another option is to use a thermal evaporator to continually evaporate a small amount of the water in the closed loop system’s volume so that fresh water can be added. Periodically, the concentrated water and salt mixture in the evaporator would also have to be hauled off. The evaporation process will reduce the total volume of waters to be hauled off, and hence, reduce the hauling cost. The third option is to use a membrane filtration system. However, this method is expensive and not at all well suited to process waters contaminated with dirt, dust, cleaning chemistries, and oils.
The salt in the waters also has implications for the components of wash water treatment systems. Although our oil water separator system is constructed of 304 stainless steel, salts in the water may attack the welds in the unit and accelerate the corrosion process. Additionally, salts will attack pump shafts and cause the seals to leak. If this happens, the only solution is to change the pump.
To combat the effects of corrosion, we offer various levels of corrosion protection to our clients. For our oil water separators, we offer an internal coating which forms a tough barrier that protects the stainless steel from the salt. For our other treatment systems, we can upgrade the pumps from carbon steel to a salt resistant 316 stainless steel, which will prevent any pitting of the shafts and pump internals. We can also add a conductivity meter to continually monitor the amount of salts and other chemicals in the water and trigger an alarm when the levels rise too high. Once this water is pumped out or discharged, fresh water is automatically added to the system, diluting the salts to a manageable level.